Practical Distillation Technology

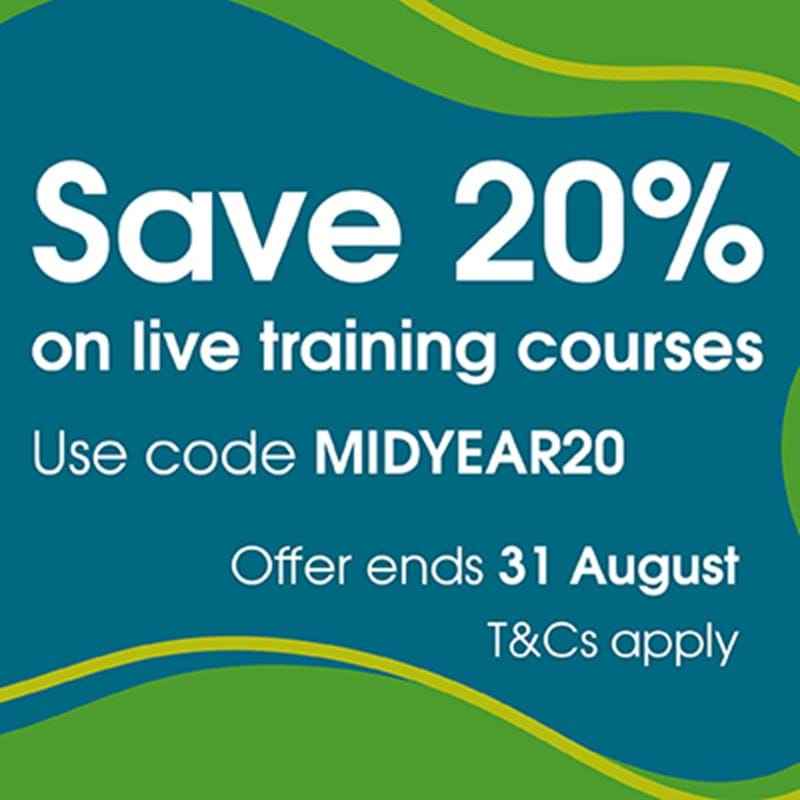
Face-to-face | In-company
Overview
Learn about distillation technology with this comprehensive course from world-renowned expert, Henry Kister.
This course has a particular emphasis on the problems that can occur and how to solve them. It will help you to develop a working knowledge of key techniques that can promote trouble-free operation and reduce distillation cost. Henry will discuss numerous operating experiences throughout the course to illustrate the key principles and to distinguish good from bad practices.
You will receive copies of two textbooks written by Henry Kister, Distillation Operation and Distillation Troubleshooting, together with extensive course materials, providing invaluable reference sources after the course.
Learning outcomes
By the end of the course, you will understand:
- how to troubleshoot a distillation column and determine what may cause poor performance
- how to evaluate existing column performance and develop new designs
- how to avoid common causes of capacity bottlenecks, tray damage, downcomer sealing problems, packed tower distributor malfunctions and many other operating difficulties
- how to de-bottleneck a column to improve capacity and/or separation
- how to control and operate a distillation column
- how to validate your tower simulation.
Who will benefit
Engineering and supervisory personnel who are involved in:
- operating
- troubleshooting
- de-bottlenecking
- designing
- starting up distillation processes.
Course outline
- Avoiding fractionation pitfalls
- Troubleshooting distillation simulations
- Tray hydraulics and limits
- Troubleshooting tray towers
- Troubleshooting packed towers
- De-bottlenecking
- Distillation control
- Avoiding tower malfunctions
- Case studies
View a detailed course outline
What delegates say
"Fantastic course with a very knowledgeable and passionate presenter, covering a wide range of useful topics. Good content, with course schedule tailored to people's interests with good use of examples to enhance understanding."
J Walton, Mitsubishi Chemical, UK
"Henry was excellent. His enthusiasm and the course content were brilliant. What a pleasure!"
E Anderson, Seqens Custom Specialties, UK
"Henry was excellent and used case-based learning effectively to demonstrate fundamental principles. The content was extremely informative and well presented. Henry's tireless energy in presenting the core material, and his willingness to answer any questions on distillation no matter how complex made this course exceptional."
S Hayton, Worley, UK
"Henry is an excellent presenter, teacher, and speaker; a terrific course."
B Floan, Crown Iron Works, USA
"Wonderful. Top class teacher."
L Ferrari, Total, Belgium
Course delivery
Online
This course is not currently delivered online.
Face-to-face
Face-to-face courses are delivered over three days.
Upcoming dates
Fees
Book any live online or face-to-face training course before 31 August and save 20%! Simply use discount code MIDYEAR20 at checkout.
- IChemE member: £2,150 + VAT
- Non-member: £2,550 + VAT
*Terms and conditions: offer applies to 2025 live online and face-to-face courses. Applies to bookings made between 1 July and 31 August 2025 and to both member and non-member prices. Cannot be used in conjunction with any other offer eg multi-place discounts. Registration must be confirmed and paid by 31 August 2025. This offer does not apply to IChemE approved courses or face to face courses in South Africa.
Contact us
+44 (0)1788 534496 / courses@icheme.org
Register your interest in future dates.
More than one person to train?
Multi-place discounts
Discounts are available to companies booking more than one place. Bookings must be made at the same time to receive the discount.
- 2 places – 10% discount
- 3 places –15% discount
- 4 or more places – 20% discount
In-company training
This course can be delivered to in-house teams, either on-site or online. This could be a cost-effective option if you have several people requiring the training. Content can be tailored to your specific requirements. Request a quotation.
Attendance certificate & CPD hours
An e-certificate will be issued at the end of the course to confirm attendance and CPD hours logged. Please note that you must attend the whole course to receive the certificate.
Associated course
Troubleshooting Distillation Controls
Learn how to get the best performance from a distillation column control system with world-renowned expert, Henry Kister.