Managing the Hazards of Flare Systems

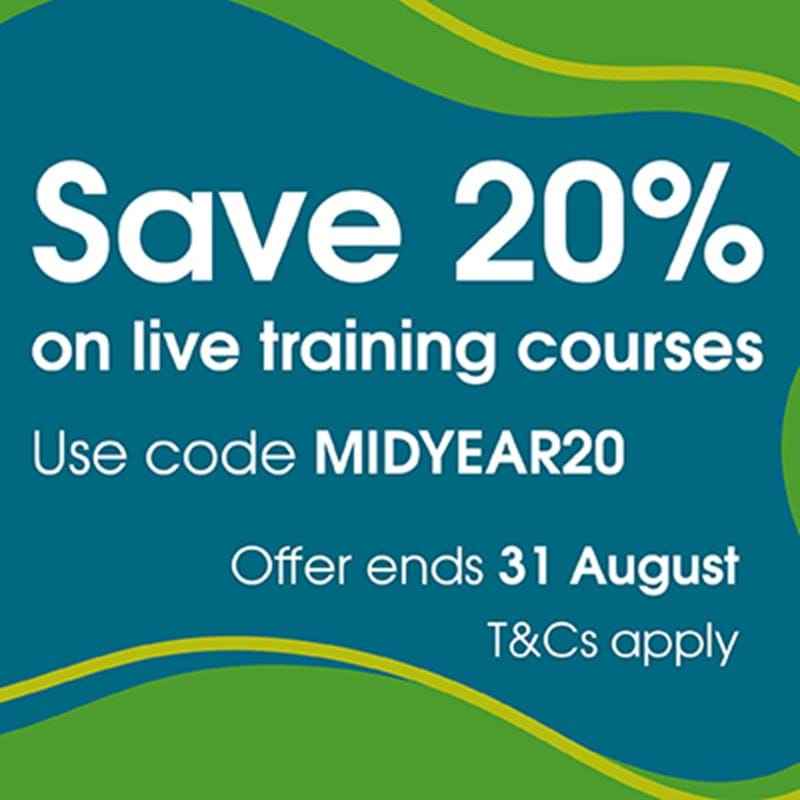
Online | Face-to-face | In-company
Overview
This course will develop your understanding of flare systems and how to control the hazards associated with them to ensure effective process safety and environmental compliance over the life cycle of a flare system.
Flare systems are used throughout the petrochemical, oil refining and upstream oil and gas industries and serve as key relief and abatement systems. However, it is crucial that they are designed, operated and maintained correctly in order to avoid accidents.
This course will give you a thorough understanding of the key design, operation, maintenance and plant modification aspects which must be controlled. It will comprehensively review the operations and equipment on all types of flare systems. It will categorise the key hazards which must be controlled, reviewing these individually, with the help of case studies of past industry accidents and incidents which demonstrate design errors only revealed in operation.
Learning outcomes
The course will help you to understand:
- the components of a flare system, how they work, why the components which make up a flare disposal system are there, and how they can fail or be rendered ineffective
- the key principles for ensuring flare system safety
- the key types of incidents and accidents and how to use this knowledge in the design, operation, modification and maintenance of flare systems
- the regulatory requirements from safety and environmental regulations such as COMAH and PPC & EPR regulations
- the general principles of flare system design.
Who will benefit
- Those who have responsibility for designing, operating, maintaining and/or modifying flare systems
- Personnel from operating companies, consultancies, EPCM companies and regulatory bodies who may be responsible for regulating assets which contain flare systems
Course outline
- Review of a flare system incident
- Review of flare system components
- Key flare system siting considerations – eg ground level heat flux criteria
- key flare system sizing considerations
- Hazard 1 – keeping air out of the flare system
- Hazard 2 – keeping flare system lit
- Hazard 3 – preventing liquid overfill
- Hazard 4 – preventing freezing/blockage
- Hazard 5 – exclusion of personnel from flare systems
- Hazard 6 – flaring toxic materials
- Hazard 7 – preventing over-chilling
- Hazard 8 – working on flare systems (live break ins where no isolation valves exist, effectiveness of isolation valves etc)
- Hazard 9 – performing operational checks, or maintenance within flare 'sterilisation' zones
- Environmental aspects of elevated flare stack systems (noise, light, loss of pilots etc)
- Other hazards (e.g. steam hammer – as steam to elevated flare headers is usually at end of a header)
Course delivery
Online
Online courses consist of two live and interactive modules with the trainer, each lasting three hours. There will also be some work to complete independently before the course and between the live sessions. More details will be provided after you have registered.
Live sessions are delivered via Microsoft Teams. If you don't already have this installed, you can join as a guest in order to access the training.
Face-to-face
Face-to-face courses are delivered over two days.
Upcoming dates
View the list of start dates on this page. To register, select your preferred course and go to the 'Book course' button.
Fees
Book any live online or face-to-face training course before 31 August and save 20%! Simply use discount code MIDYEAR20 at checkout.
- IChemE member: £880 + VAT
- Non-member: £1,100 + VAT
*Terms and conditions: offer applies to 2025 live online and face-to-face courses. Applies to bookings made between 1 July and 31 August 2025 and to both member and non-member prices. Cannot be used in conjunction with any other offer eg multi-place discounts. Registration must be confirmed and paid by 31 August 2025. This offer does not apply to IChemE approved courses or face to face courses in South Africa.
Contact us
+44 (0)1788 534496 / courses@icheme.org
Register your interest in future dates.
More than one person to train?
Multi-place discounts
Discounts are available to companies booking more than one place. Bookings must be made at the same time to receive the discount.
- 2 places – 10% discount
- 3 places –15% discount
- 4 or more places – 20% discount
In-company training
This course can be delivered to in-house teams, either on-site or online. This could be a cost-effective option if you have several people requiring the training. Content can be tailored to your specific requirements. Request a quotation.
Attendance certificate & CPD hours
An e-certificate will be issued at the end of the course to confirm attendance and CPD hours logged. Please note that you must attend the whole course to receive the certificate.
In the case of online courses, CPD hours should be used as an approximate guide and will vary depending on the preferred approach of the delegate and to what extent additional learning is completed.
Associated courses
Comprehensive Explosion Science
Understand the phenomenon and consequences of explosions on industrial premises that fall under the DSEAR and ATEX regulations.
Hazard Identification Techniques
Discover key techniques that can be used to identify process safety risks.
Process Risk Assessment
Learn about the risk assessment techniques used in the process industries.