#Hazards29 – Leading the way forward in process safety by sharing learnings
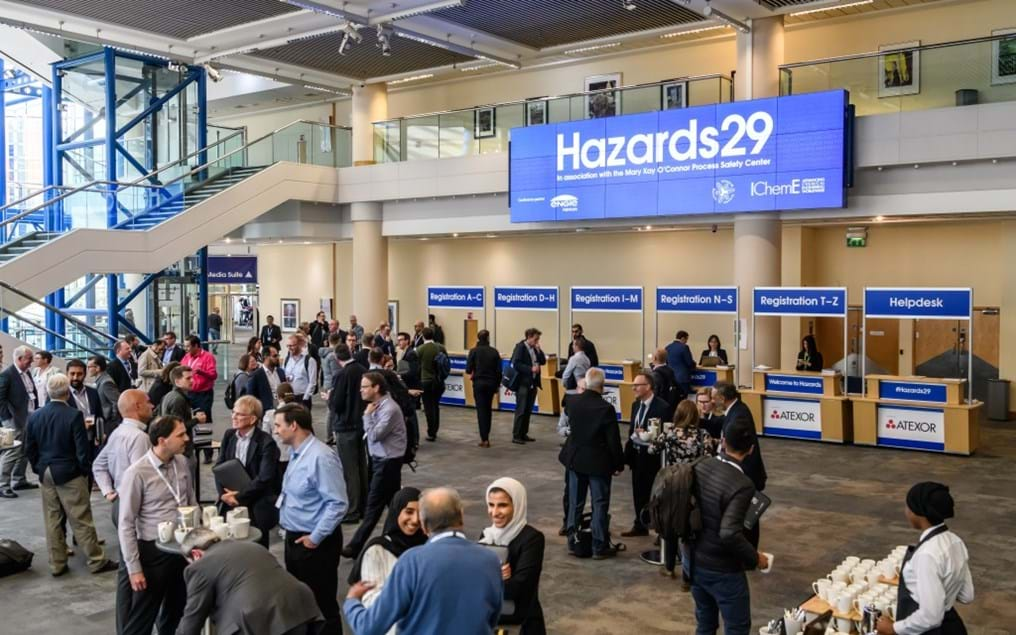
31st May 2019
Last week more than 300 leading industry experts and process safety professionals from around the world attended IChemE’s leading process safety conference, Hazards 29 in Birmingham, UK.
They came together to share knowledge and their learnings from process safety incidents through a range of plenary talks, parallel sessions and workshops.
The message throughout was clear: process safety is a continued priority for all concerned. Sharing experiences, better risk management and competency are integral to mitigating hazards, and improving process safety procedures.
Here are some of our key takeaways from the conference.
Safety begins with me
Walt Disney’s safety philosophy
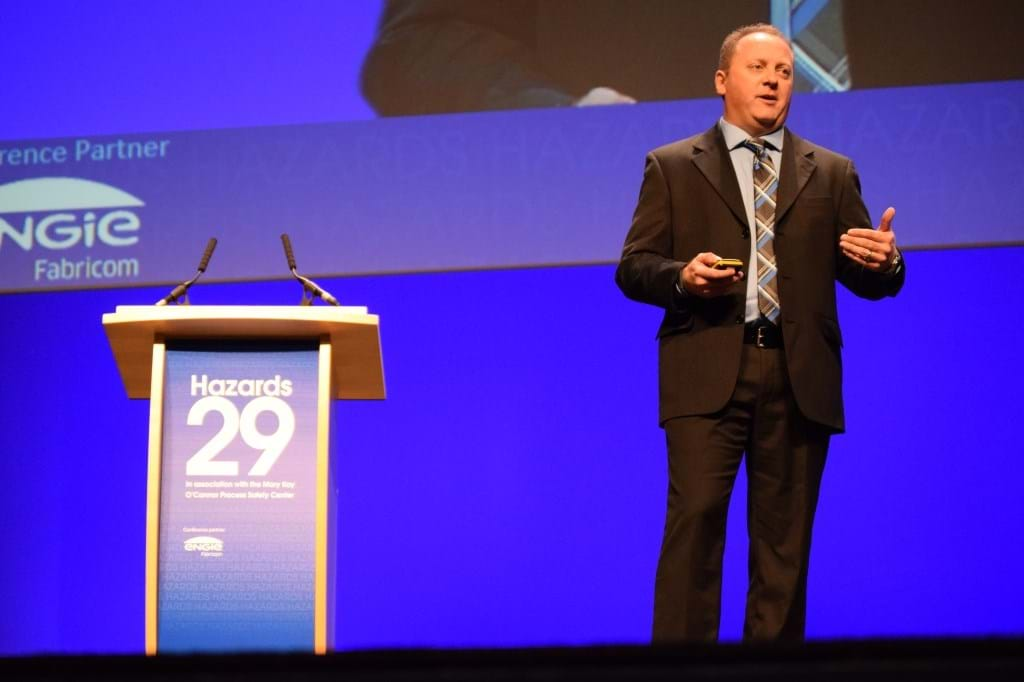
With over 1 billion rides per year, six parks, 784 camp sites, 27,945 rooms and 74,000 cast members, the risks involved for a theme park of its magnitude requires a watertight operation to ensure the guest experience is not only safe, but an enjoyable and memorable one too.
Health and safety training is provided in several languages, and a simple, visual hazards matrix tool was developed for cast members to manage hazards. Everything at Disney is underpinned by a culture empowering the employees to take ownership of safety. To run a safe operation, they adopt the ‘four keys’: courtesy, show, efficiency and safety.
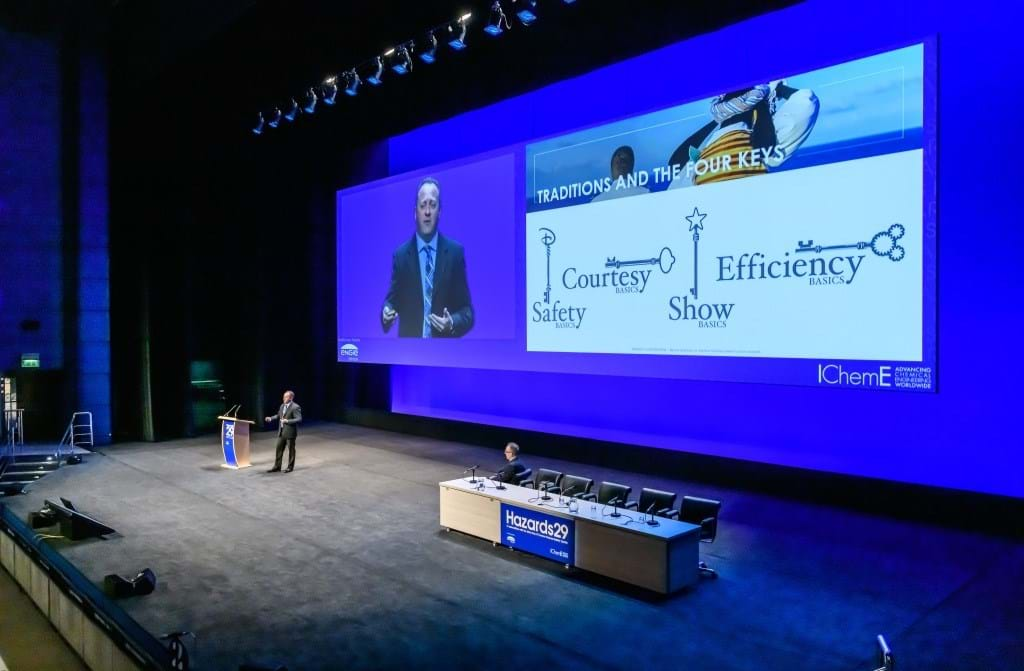
He described the many unconventional risks that could arise at Disney’s parks and resorts. From, the rides and rollercoasters to animatronics and mechanical character suits; choreographed stunt shows, and safely handling animals to pyrotechnics and laser displays - these all require robust and unique procedures.
Live stunt shows, including high rise falls and motor vehicles with fire, can be performed up to nine times a day. These are highly choreographed and scrutinised to ensure safe landings are performed and cast can have up to five layers of protective clothing for safety and durability throughout the shows.
Specialised silicone materials are developed for costumes, such as for Grut from Guardians of the Galaxy and a 10ft tall mechanical utility suit for an Avatar character, to be ergonomic, light weight, and breathable. Bell said they are so light weight they could blow over, so weather protocols have been put in place, and safety staff accompany the cast members to maintain safety.
They also use the Swiss cheese model to analyse and mitigate hazards, and put in layers of protection and security. However, Disney have seen new and unexpected threats with the rise in social media. They’ve put measures in for guests and are continually monitoring for potential new risks.
With so many unconventional risks, Bell concludes it everyone’s responsibility of everyone to ensure incidents can be prevented.
He said: “Now we’re seeing more and more people wanting to take shots from cool areas and angles to put on social media, so they’re climbing up on our props. It’s the potential to fall that’s the risk. So we’ve built climb resistance props and improved our internal standards to avoid people climbing and falling.
“Our cast and our customers need to see that safety is critical and be part of the solution.”
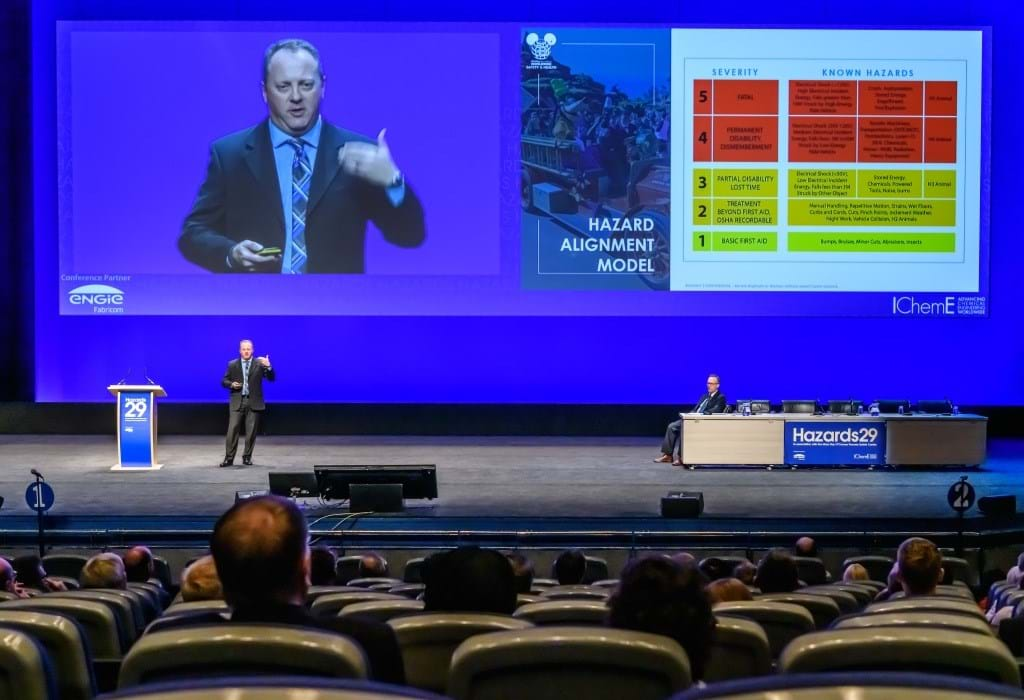
Question your decision-making to seek alternative choices to enhance process safety
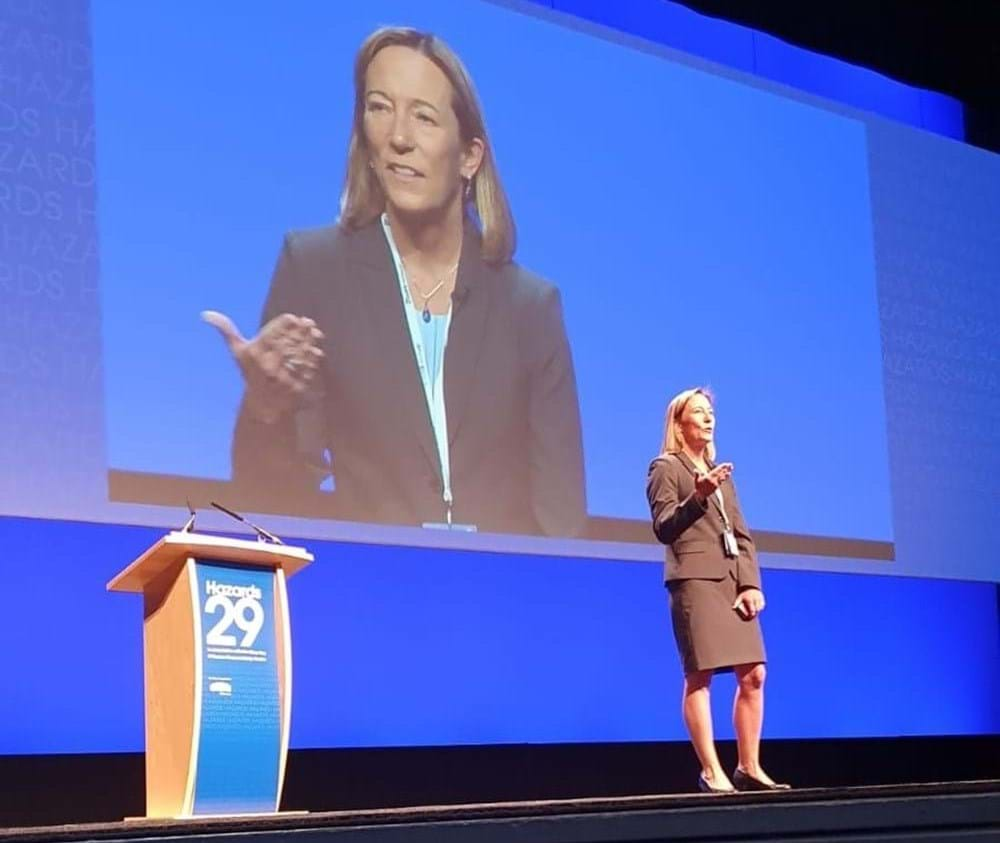
She asked process safety engineers to consider thinking beyond the idea of having just one correct answer or choice, and to embrace ways of thinking that challenge the status quo.
Demonstrating through personal and professional examples, she urged delegates to think about how they can add ‘And’ in their conversations to identify causes and impacting factors of incidents, to ensure these can be mitigated in future.
She said: “I want to challenge leaders to say ‘And’, in order to figure out the leading indicators and prevent the next incident, so that you don’t have to experience it the way I did.’’
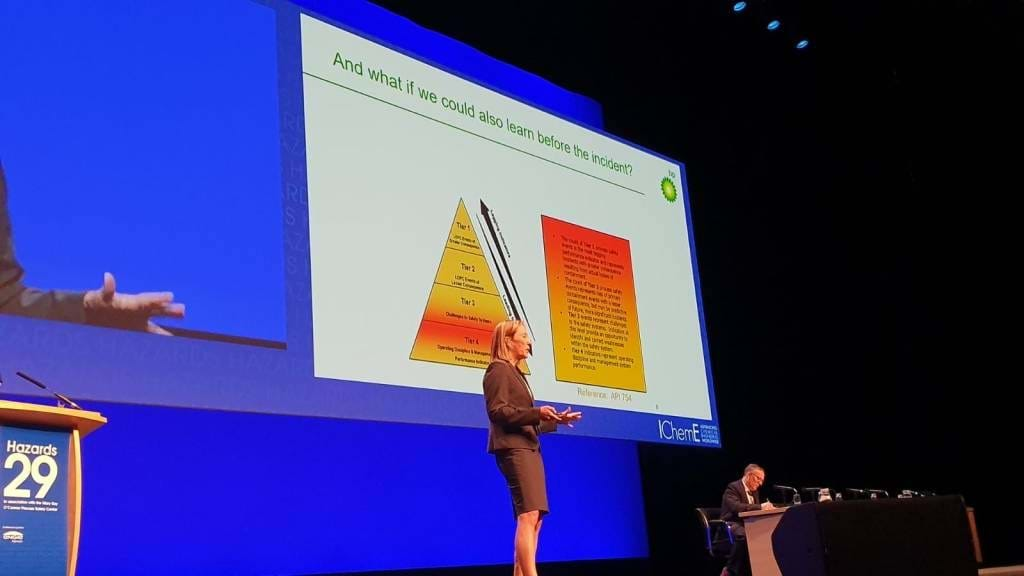
“…‘And’ what are we going to do to make sure those who have not had the horrific experience of dealing with a process safety incident will never have to.”
Achieving, maintaining and demonstrating competencies for process safety
A new interactive panel discussion was introduced at Hazards 29 allowing delegates to ask panellists questions on the topic: How do we achieve, maintain and demonstrate competencies for process safety?
The questions led to thought-provoking discussions between the panelists Dame Judith Hackitt, Chair of EEF; IChemE President Ken Rivers; Trish Kerin, Director, IChemE Safety Centre; Chris Tighe, Imperial College London; Consultant Ken Pattison, and Matthew Powell-Howard, NEBOSH.
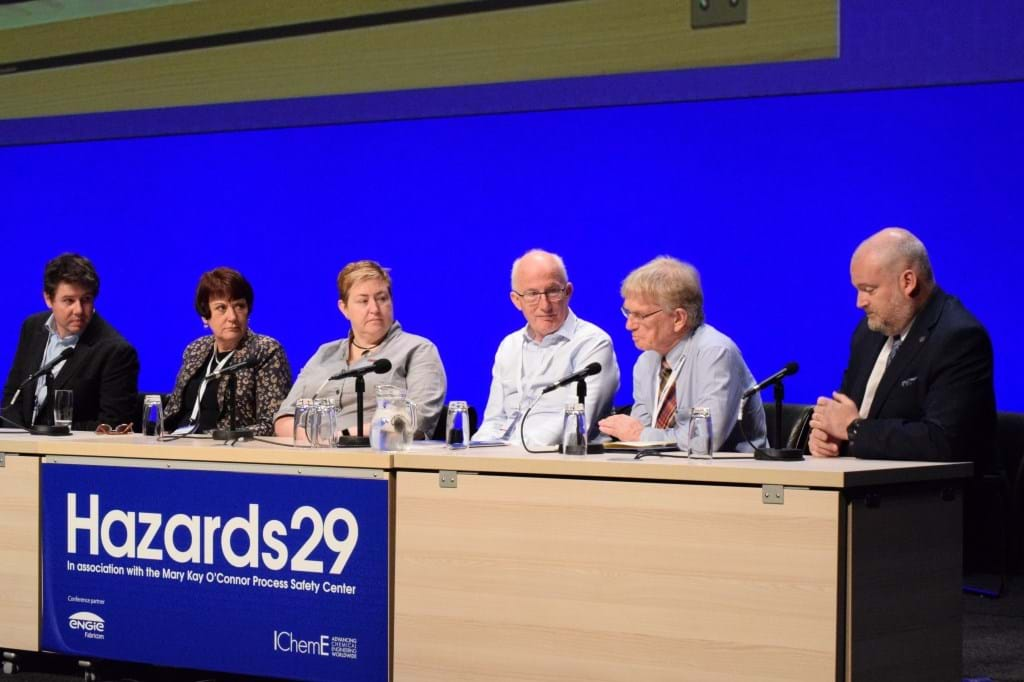
Rivers said: “The thing that keeps me competent is that whenever there is an incident, I ask myself, ‘How have I been complicit in this?’ Continuously asking myself has changed my look towards process safety.”
“We all have to work collaboratively. It goes far beyond that process safety competence is just for chemical engineers. It’s about getting companies to share their competencies,” said Kerin.
Hackitt added: “We’ve got to get organisations sharing and engineering institutions working and sharing together.”
The underlining message from all was the need for more dialogue between process safety experts, and encouraging the sharing of stories to learn from past experiences, and identifying ways to work together to become more competent in process safety overall.
Process safety tributes
Tributes were also paid to pioneering process safety engineers, Professor Hans Michels, Imperial College London, Kevin Dixon-Jackson, Ciba, and Sam Mannan, Executive Director of the Mary Kay O’Connor Process Safety Center (MKOPSC), who have recently passed away.
This year’s Poster Prize was renamed in Mannan’s honour and saw 25 poster presentations on process safety ideas and innovations.
Sinead Keophane and Brenda Madden, PM Group, won the prize for their poster, which highlights a gap in the EU legislative framework for potential Major Accident Hazards.
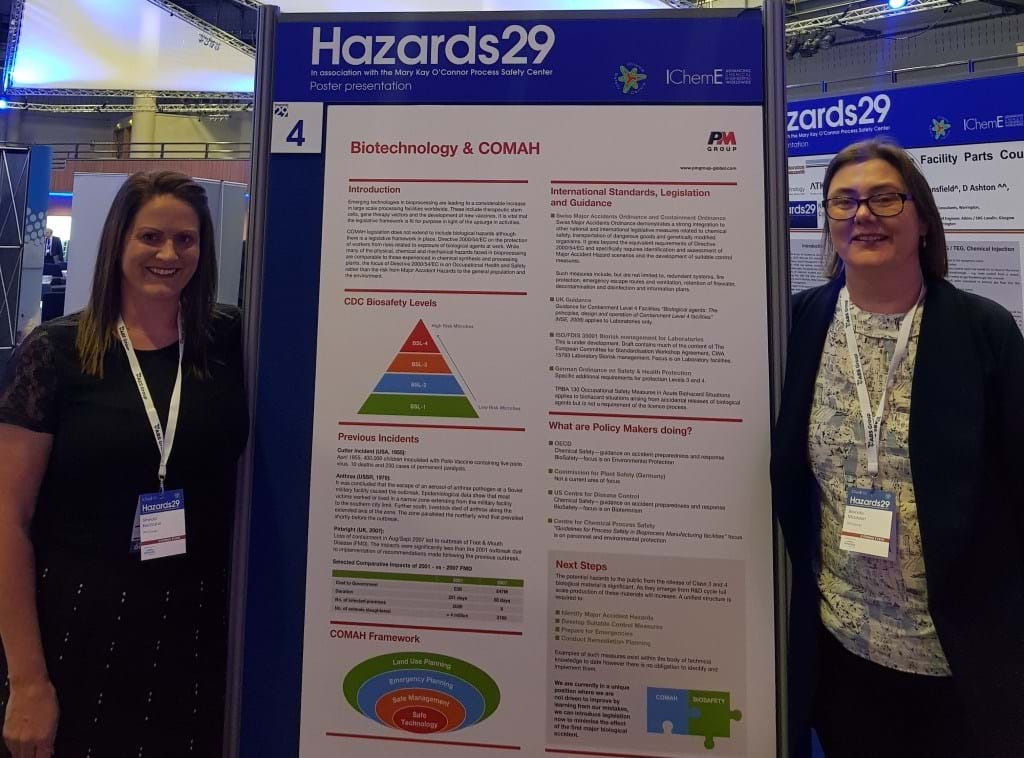
Throughout the conference, representatives from IChemE and the IChemE Safety Centre interacted with delegates to explain more on the process safety resources available through IChemE membership, including the Loss Prevention Bulletin, IChemE Safety Centre case studies, and relevant training courses, to name but a few.
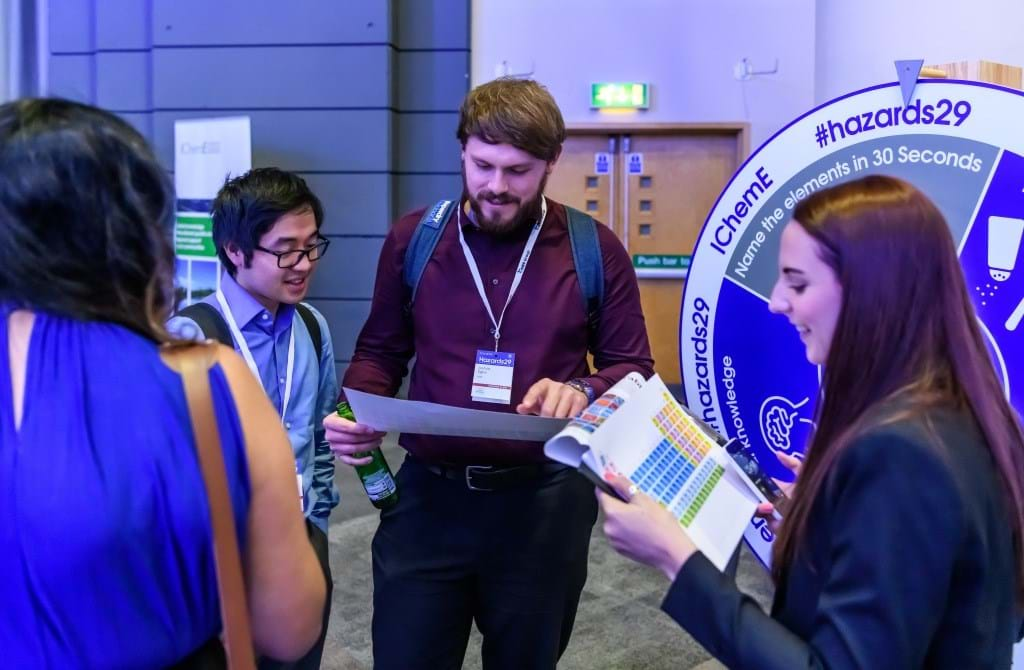
You can see all our photos from the conference in our albums on Flickr.
Help us continue sharing knowledge and lessons learned in process safety by joining us next year at Hazards 30, from 18-20 May 2020 in Manchester, UK.